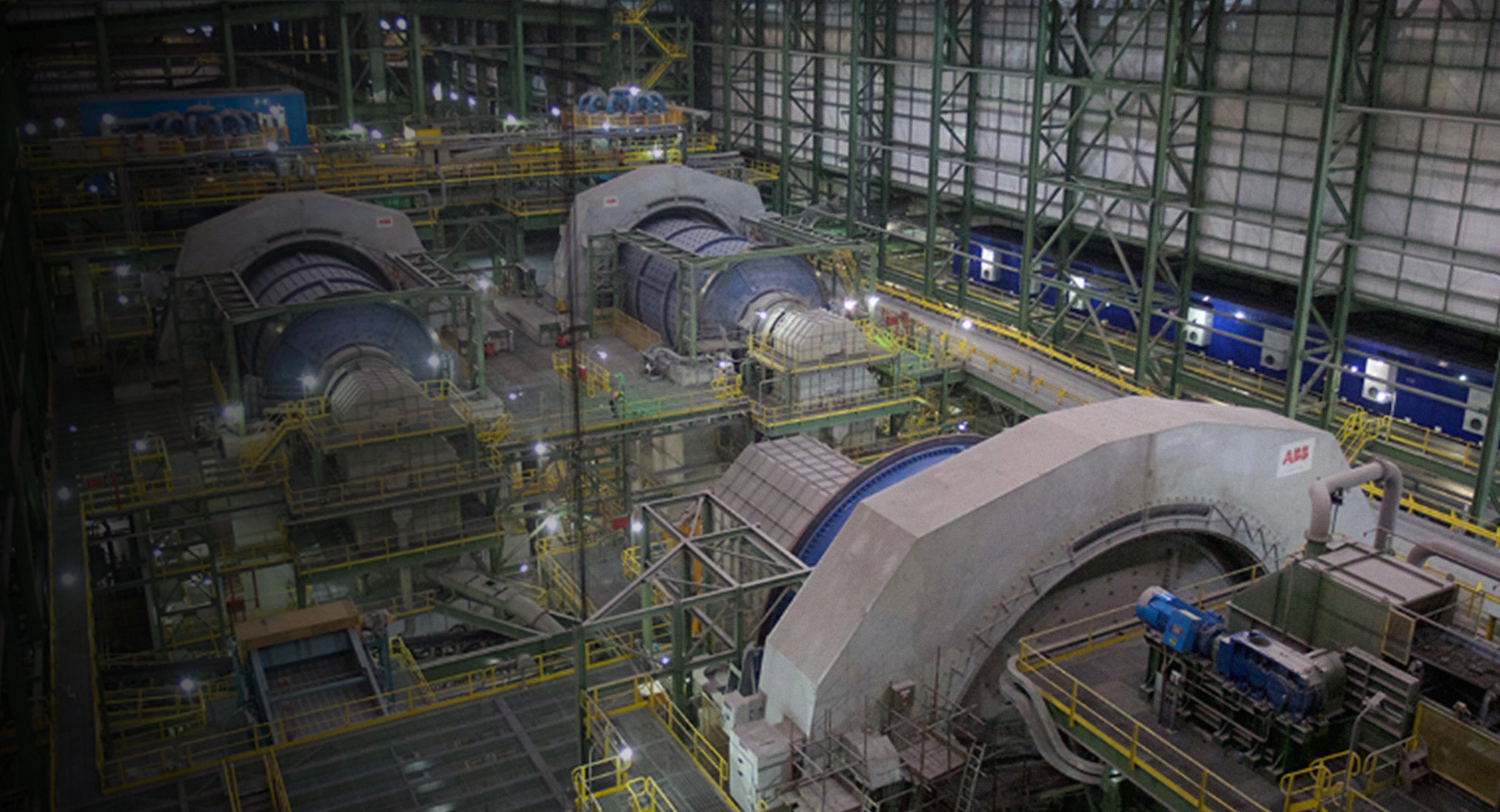
Project: Copper Mine
Location: Kazakhstan
Overview
The comminution flowsheet consists of a primary gyratory crusher feeding an open circuit SAG mill with forward pebble crushing (2x cone crushers followed by a closed circuit HPGR). SAG mill discharge and HPGR product feeds two ball mills in closed circuit with cyclones.
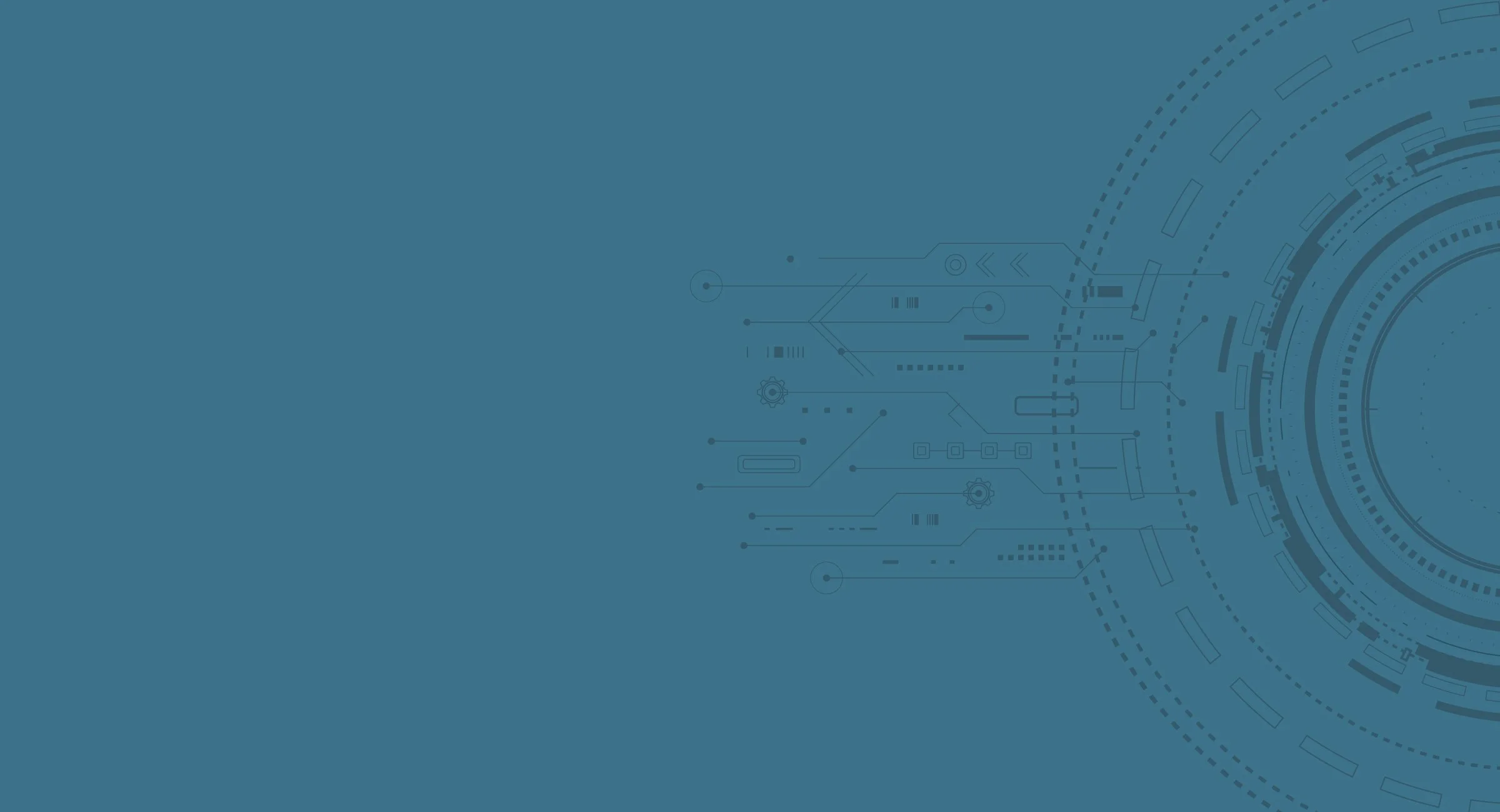
The Challenge
To assist site to optimise and stabilise circuit performance above design levels. A grinding circuit review was carried out and found that:
Process control philosophy needed to be optimised with SAG mill load control and cyclone efficiency sub-optimal.
Power utilisation and energy intensity were underutilised.
HPGR pebble crushing was underutilised.
The MillROC Solution
Recommendations were put in place for the installation of MillROC with a MillSlicer.
An improved process control strategy was implemented with site and the APC vendor stabilising cyclone pressure, SAG mill weight and optimising mill speed.
Training of operations to understand the theory of operation and the process control philosophy.
A program of continually reviewing results and coaching using MillROC for continuous optimisation was implemented.
Outcomes
Improvement to the philosophy and tuning of the control system resulted in more robust operation with seamless and rapid switching between soft and hard ore operating regimes providing continual, optimal performance.
During the project, the focus shifted from realising circuit benefits to reliably achieving the nameplate capacity and further to targeting larger circuit upgrades and optimisations, exceeding design.
Overall, the average circuit throughput increased 15% from 3,300tph to over 3,800tph due to improved process control, set-point selection and power utilisation, despite sporadic increases in the ore hardness.